Regulatory compliance is an important component of MRE (Meal, Ready-to-Eat) production, guaranteeing adherence to food safety regulations to safeguard consumers.
This article delves into the specifics of regulatory compliance in the manufacturing of MREs, outlining the responsibilities of the FDA and USDA and the procedures necessary to maintain compliance.
Exploring the significance of regulatory compliance, the repercussions of non-compliance, and methods for MRE producers to remain informed about regulatory modifications, we examine the intricacies of regulatory compliance in MRE production.
What Is Regulatory Compliance in MRE Production?
Regulatory compliance in MRE (Meal, Ready-to-Eat) production involves adhering to specific legal requirements, government standards, and health and safety guidelines established by regulatory agencies. It includes following strict processes and protocols to ensure that MREs meet the required quality control and food safety regulations.
Maintaining regulatory compliance is crucial in the MRE industry to protect consumer health and uphold the integrity of the supply chain. Compliance officers have a key role in supervising the enforcement of these regulations within production facilities. These professionals stay informed about the continually changing food safety laws and industry standards, collaborating closely with regulatory agencies to address any compliance issues.
Regulatory agencies, such as the FDA and USDA, work diligently to monitor and enforce compliance with these regulations, conducting inspections and audits to uphold the safety and quality of MRE products.
Why Is Regulatory Compliance Important in MRE Production?
Regulatory compliance is essential in MRE production to protect public health and assure the quality and safety of food products. By following health and safety guidelines and undergoing compliance monitoring, MRE producers reduce the risks of penalties for non-compliance and foodborne illnesses.
This dedication to regulatory compliance extends beyond mere rule adherence; it signifies a commitment to transparency, integrity, and accountability within the industry. Upholding these standards not only safeguards consumers but also cultivates trust and confidence in the integrity of MRE products. Compliance ensures that proper labeling, sourcing, and handling practices are observed, ensuring the traceability and authenticity of ingredients.
Consequently, MRE manufacturers play a crucial role in promoting consumer protection and advancing public health initiatives through their steadfast dedication to regulatory compliance.
What Are the Food Safety Regulations for MRE Production?
Food safety regulations for MRE production encompass strict requirements related to manufacturing practices, product labeling, and contamination prevention measures. Compliance with these regulations is crucial to maintain quality assurance standards and prevent foodborne illnesses. Adherence to manufacturing practices involves following precise guidelines for ingredient sourcing, processing, and storage to uphold the highest food safety standards.
Product labeling requirements ensure clear and accurate information for consumers regarding ingredients, allergens, and nutritional content. Contamination prevention protocols include rigorous sanitation procedures, regular equipment maintenance, and monitoring of production environments to minimize the risk of microbial or chemical hazards in MREs. These regulations serve as a vital framework to protect consumer health and uphold the integrity of MRE products.
What Is the Role of the FDA in MRE Production?
The FDA (Food and Drug Administration) is involved in overseeing inspection procedures, certification processes, and compliance audits related to MRE (Meal, Ready-to-Eat) production. This oversight is carried out to ensure that MREs meet the required regulatory standards.
These responsibilities are crucial for protecting public health and ensuring the safety of food products consumed by individuals. The FDA conducts thorough inspection procedures to assess MRE facilities and confirm their compliance with good manufacturing practices and hygiene standards. Certification processes involve detailed examinations of product formulations, labeling, and packaging to verify adherence to labeling requirements and ingredient specifications. Compliance audits are also performed to monitor ongoing compliance with FDA regulations and address any identified non-compliance issues promptly.
What Is the Role of the USDA in MRE Production?
The United States Department of Agriculture (USDA) is involved in MRE (Meals Ready-to-Eat) production by overseeing ingredient sourcing, supply chain management, and ensuring compliance with government standards to uphold the safety and quality of MREs.
By actively monitoring ingredient sourcing, the USDA ensures that MRE manufacturers follow strict government guidelines to preserve the nutritional value and safety of these meals. The USDA also plays a crucial role in overseeing the supply chain of MRE production, from obtaining raw materials to distributing the final products, to maintain a smooth and effective process.
Through thorough inspections and audits, the USDA enforces strict regulations to prevent any inconsistencies or deviations from quality standards in MRE production.
What Are the Steps to Ensure Regulatory Compliance in MRE Production?
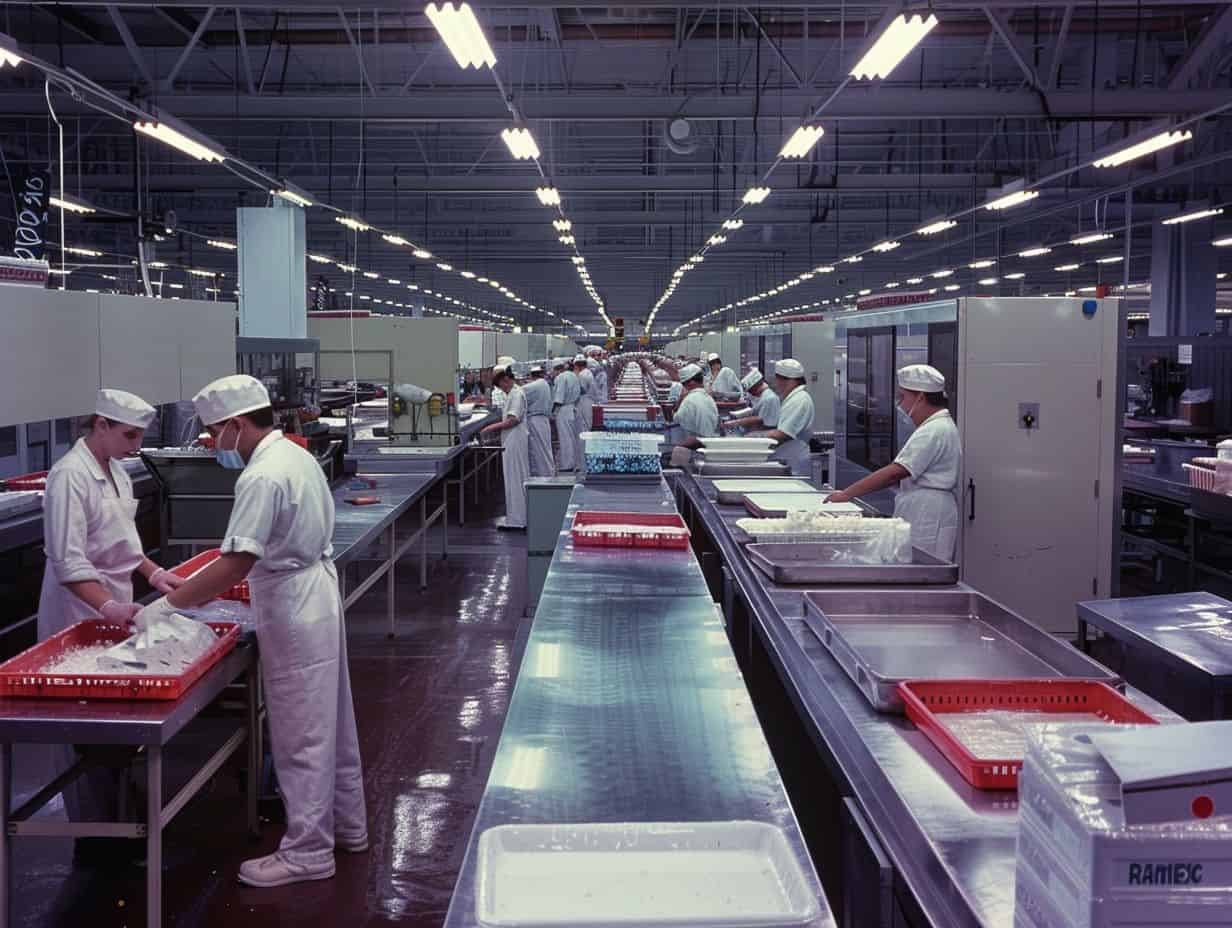
Ensuring regulatory compliance in MRE production involves several key steps such as conducting thorough risk assessments, maintaining detailed documentation, and developing comprehensive emergency response plans. These steps are crucial for upholding compliance with legal requirements and industry standards.
Risk assessments are essential for identifying and understanding potential hazards in the production process. By evaluating risks associated with each stage of manufacturing, MRE producers can proactively address safety concerns. Documentation plays a critical role in demonstrating adherence to regulations, with accurate records aiding in audits and inspections. Effective emergency response plans ensure that workers are prepared to handle unforeseen events, minimizing damage and ensuring quick resolution. Combining these elements creates a robust framework that not only meets compliance but also prioritizes the safety and well-being of employees and consumers.
1. Conducting Hazard Analysis
In MRE production, conducting a hazard analysis involves identifying and assessing potential risks and hazards to ensure compliance with regulatory standards and undergo thorough compliance audits.
This essential process follows a systematic approach to evaluate every stage of production, from ingredient sourcing to final packaging, to identify any potential dangers or risks. By conducting a hazard analysis, MRE producers can proactively mitigate risks and prioritize safety measures to ensure that the products meet quality and safety standards.
Risk assessment plays a key role in determining the likelihood and severity of identified hazards, allowing companies to adjust their safety protocols accordingly. Compliance audits act as important checkpoints to verify that the hazard analysis procedures are consistently followed and regulatory requirements are met.
2. Implementing Preventive Controls
Implementing preventive controls in MRE production is crucial for preventing contamination, ensuring product safety, and conducting rigorous product testing to adhere to food safety regulations.
By incorporating preventive measures, MRE manufacturers can significantly reduce the risk of microbial contamination, which can pose serious health risks if consumed. These controls involve implementing strict sanitation protocols, regular equipment maintenance, and thorough employee training to eliminate sources of contamination.
Conducting comprehensive product testing further ensures the quality and safety of MREs before they are distributed to consumers, building trust and loyalty in the brand. Prioritizing preventive controls in the production process is not only a regulatory requirement but also a critical measure in safeguarding consumer health and satisfaction.
3. Monitoring and Record-Keeping
Monitoring and record-keeping practices in MRE production involve maintaining detailed records, implementing a traceability system, and ensuring compliance with regulatory standards to effectively track the production process.
The significance of these practices is crucial, as they serve as the foundation of quality assurance and food safety in the MRE industry. By documenting every step of the production chain meticulously, producers can promptly identify any issues that may arise and take corrective actions. Traceability systems allow for the quick identification of the origin of raw materials or any potential contaminants, promoting transparency and accountability within the supply chain. This level of detailed record-keeping not only improves product quality but also establishes consumer trust by showcasing a dedication to excellence.
4. Taking Corrective Actions
Addressing deviations from regulatory compliance in MRE production involves taking corrective actions promptly, undergoing compliance monitoring, and implementing measures to rectify non-compliance issues.
It is crucial to establish a systematic approach to identify potential non-compliance areas, such as conducting regular audits and inspections to ensure adherence to established guidelines.
Once deviations are identified, immediate action must be taken to investigate the root cause and develop a corrective action plan. This plan should include specific steps to address the issues, assign responsibility for implementation, and establish a timeline for completion.
Monitoring the effectiveness of these corrective measures is vital to prevent recurrence and maintain continuous improvement in MRE production processes.
5. Verifying Compliance through Inspections and Audits
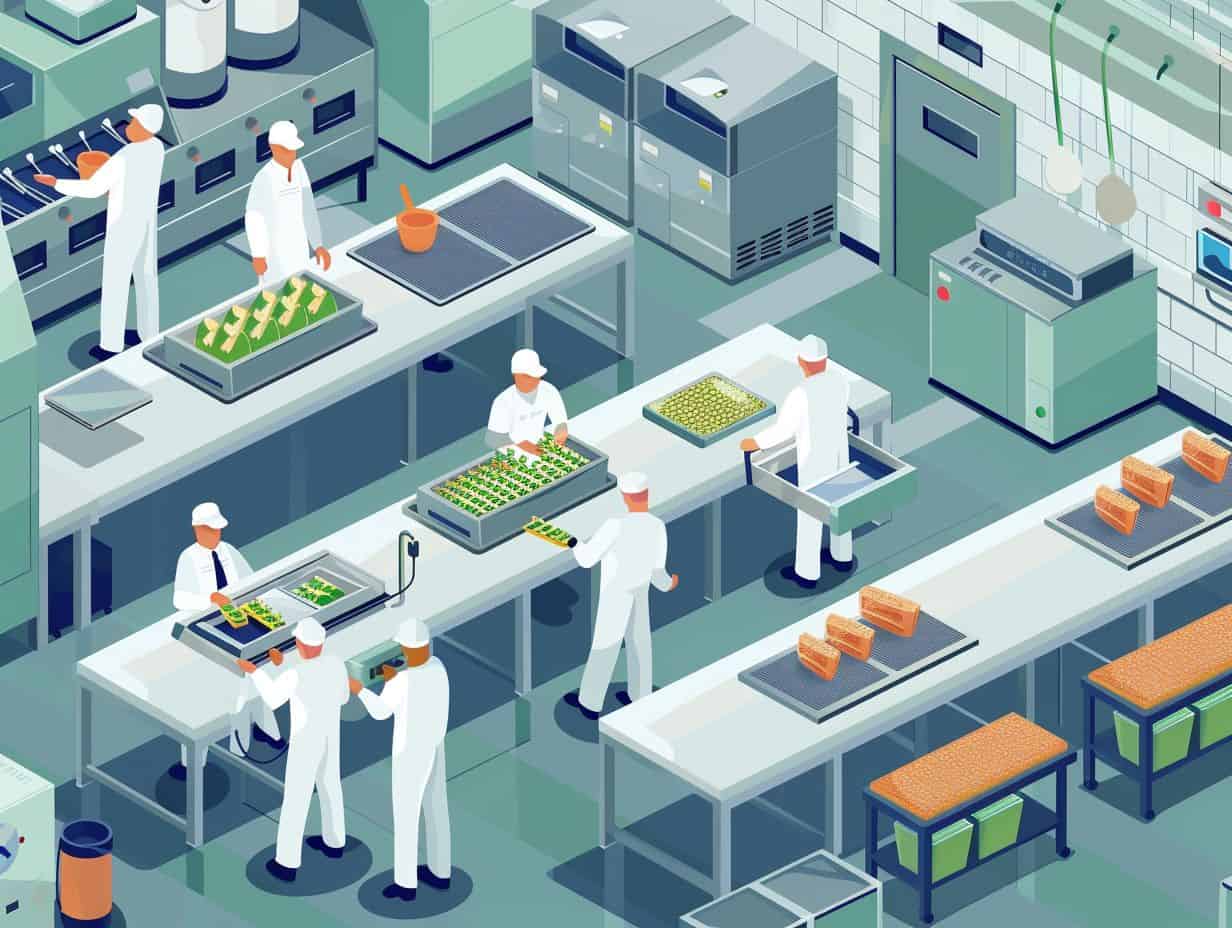
Verifying compliance in MRE production involves conducting thorough compliance audits, implementing inspection procedures, and monitoring compliance to ensure adherence to regulatory standards.
Ensuring compliance in MRE production is crucial for maintaining product safety and quality. By regularly conducting compliance audits, companies can identify and address any potential deviations from regulations that could compromise the integrity of the products. Inspection procedures play a key role in verifying that production processes align with industry standards and best practices. These audits and inspections not only safeguard consumer health but also contribute to building trust and credibility in the market. Continuous monitoring of compliance allows for prompt corrective actions and improvements to maintain a high level of regulatory adherence.
What Are the Consequences of Non-Compliance in MRE Production?
Non-compliance in MRE production can lead to serious consequences such as non-compliance penalties, product recalls, and the necessity for crisis management to minimize the impact on consumer protection and public health.
Failure to conform to regulatory standards in the MRE industry can result in substantial financial losses for companies, damaging their reputation and diminishing consumer trust. Product recalls stemming from non-compliance present risks to public health and safety, potentially leading to legal actions and lawsuits. Effective crisis management becomes essential in such scenarios to manage the repercussions and rebuild confidence among consumers and stakeholders, underscoring the vital significance of upholding compliance in MRE production processes.
1. Fines and Penalties
Fines and penalties for non-compliance in MRE production can lead to significant financial repercussions, regulatory sanctions, and increased scrutiny through compliance monitoring.
For businesses involved in MRE production, the consequences of failing to adhere to regulatory standards can be severe. Not only do fines and penalties impact the company’s bottom line, but they also tarnish its reputation in the industry. The imposition of fines may result in costly legal battles and diminished consumer trust. Regulatory bodies closely monitor non-compliant entities, subjecting them to stricter oversight and potential operational restrictions. Thus, maintaining compliance with MRE production guidelines is crucial to avoid these detrimental effects.
2. Product Recalls
Product recalls in MRE production are initiated in response to contamination risks, regulatory updates, or quality control issues to prevent consumer exposure to unsafe products and uphold compliance with food safety regulations.
Contamination risks in MRE production can arise from various sources such as improper handling of ingredients, cross-contamination during processing, or inadequate packaging. Even a small oversight in the production chain can lead to microbiological, chemical, or physical contamination of the final product, posing serious health risks to consumers.
Regulatory updates play a crucial role in ensuring that manufacturers stay current with food safety standards and guidelines, prompting them to take swift action in the event of any potential risks to public health. Quality control issues, like irregularities in ingredient sourcing or production methods, also necessitate timely recalls to maintain the integrity and trustworthiness of the brand.
3. Damage to Reputation
Failure to comply with MRE (Meals Ready-to-Eat) production standards can have serious repercussions on the producer’s reputation, affecting consumer trust, public perception of health, and requiring effective crisis management strategies.
Instances of non-compliance can weaken consumer confidence, raise concerns about product safety, and subject the company to scrutiny. In the food industry, reputation is closely linked to how public health is perceived, as any negative incidents can result in a significant loss of trust from consumers.
During such times, prompt and transparent crisis management is essential to minimize the impact, rebuild trust in the brand, and reassure the public that steps have been taken to maintain quality standards.
How Can MRE Producers Stay Up-to-Date with Regulatory Changes?
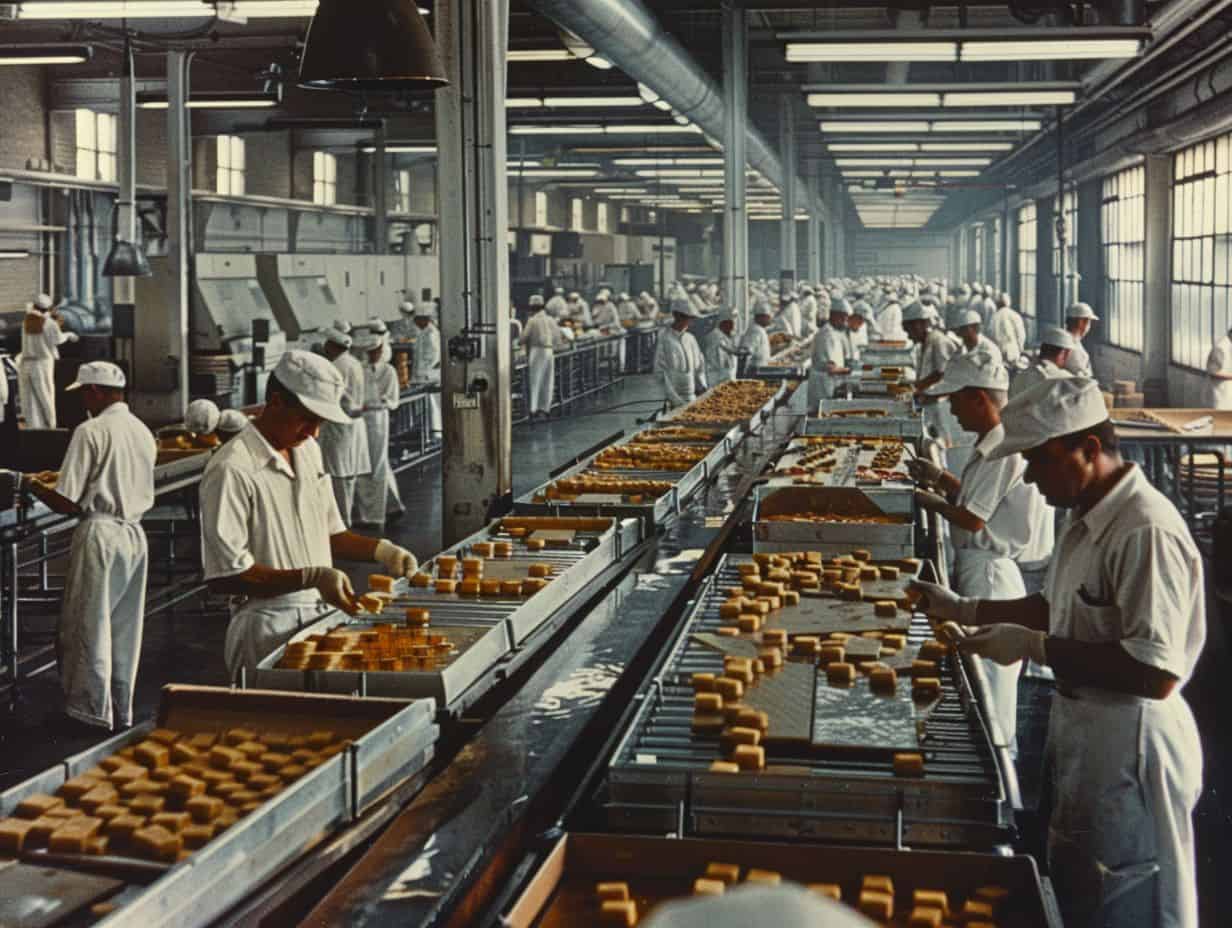
MRE producers can maintain awareness of regulatory changes by instituting robust training programs, cultivating a culture of continuous improvement, and routinely monitoring regulatory updates to ensure ongoing conformity with evolving standards.
This proactive approach not only aids in adhering to current regulations but also enables producers to anticipate and prepare for future changes. Training programs play a crucial role in educating staff about relevant regulations, ensuring that everyone is well-informed about compliance requirements. By encouraging a culture of continuous improvement, companies can establish an environment where employees are actively involved in remaining informed and implementing best practices. Embracing a mindset of continuous learning and adaptation is crucial in a dynamic regulatory landscape, allowing MRE producers to effectively navigate challenges.
Frequently Asked Questions
What are the regulations that MRE production companies need to comply with?
MRE production companies need to comply with various regulations, including the Food Safety Modernization Act (FSMA), Good Manufacturing Practices (GMP), and Hazard Analysis and Critical Control Points (HACCP) to ensure the safety of their products.
How does the FSMA impact MRE production companies?
The FSMA was enacted to shift the focus of food safety from responding to contamination to preventing it. MRE production companies must comply with FSMA regulations to ensure that their products are safe for consumption.
What is the role of GMP in MRE production?
GMP regulations set standards for the production, packaging, labeling, and storage of food products, including MREs. It ensures that all aspects of the production process are in compliance with food safety regulations.
Why is HACCP important for MRE production?
HACCP is a systematic approach to identifying and preventing potential hazards in the food production process. MRE production companies must have a HACCP plan in place to ensure the safety of their products and comply with food safety regulations.
What are the consequences of non-compliance with food safety regulations in MRE production?
Non-compliance with food safety regulations can result in product recalls, fines, and damage to the company’s reputation. It can also lead to foodborne illnesses in consumers, causing serious health risks.
How can MRE production companies ensure continuous compliance with food safety regulations?
MRE production companies can ensure continuous compliance with food safety regulations by regularly reviewing and updating their food safety plans and procedures, conducting regular training for employees, and implementing quality control measures throughout the production process.