Curious about the latest advancements in MRE manufacturing technologies?
This article explores the evolution of MRE production, from traditional methods to cutting-edge innovations like 3D printing and high-pressure processing.
It delves into the benefits of these new technologies, as well as the challenges and limitations they present.
Join in the discussion of the future of MRE manufacturing, including the integration of artificial intelligence, sustainable solutions, and improved nutrition.
What are MREs?
The Meal, Ready-to-Eat (MRE) is a self-contained, individual ration that is lightweight, portable, and easy to consume. These meals are commonly utilized by military personnel, outdoor enthusiasts, and emergency response teams.
MREs are designed to offer a balanced and nutritious meal that can be quickly prepared with minimal resources and equipment. Innovative manufacturing technologies, such as retort pouches and freeze-drying methods, are integrated to ensure MREs have a long shelf life and maintain their quality. Stringent quality control measures are implemented throughout the manufacturing process to guarantee each meal meets safety standards and nutritional requirements. In response to the growing emphasis on sustainability in food production, efforts are being made to improve the eco-friendliness of MRE packaging materials.
How are MREs Manufactured?
MREs undergo a detailed manufacturing process that includes sourcing high-quality ingredients, creating specialized recipes, and using advanced manufacturing technologies for packaging and preservation.
After selecting ingredients, the next stage involves formulating the recipe with precise measurements and proportions to maintain nutritional value, taste, and shelf life of the MREs. Collaboration between food scientists, nutritionists, and culinary experts is common to ensure a well-balanced and appealing meal.
Modern production techniques like extrusion and freeze-drying are employed to convert ingredients into compact, lightweight meals that preserve flavor and texture. Quality control measures are in place at each step, with automated systems monitoring variables such as temperature, moisture levels, and packaging integrity to ensure product safety and consistency.
What are the Traditional Manufacturing Technologies for MREs?
Traditional manufacturing technologies for MREs have developed over time, incorporating methods such as canning, dehydrating, and retort pouch packaging to ensure food preservation and shelf stability. These techniques have a historical background, with canning dating back to the early 19th century as a crucial method for extending the shelf life of perishable goods. Dehydration, another important process in MRE production, has roots tracing back to ancient civilizations’ efforts to preserve food. Over the years, advancements in technology have allowed for more efficient and precise manufacturing processes, resulting in MREs that meet industry standards for safety and quality while also catering to diverse consumer preferences.
What are the Limitations of Traditional Manufacturing Technologies for MREs?
Despite their reliability, traditional manufacturing technologies for MREs encounter difficulties in preserving freshness, flavor, and nutritional content over prolonged storage periods, potentially resulting in quality deterioration.
This issue is particularly significant in the contexts of military operations, emergency relief efforts, and outdoor recreational activities, where MREs play a vital role as a food source. The shelf-life restrictions inherent in conventional manufacturing methods restrict the length of time MREs can remain viable, creating logistical hurdles and potentially compromising the nutritional quality of the food. Traditional procedures can lead to nutrient loss during preparation and packaging, affecting the overall health benefits that MREs are designed to offer.
What are the Innovative Technologies for MRE Manufacturing?
Innovative technologies have transformed MRE manufacturing, introducing advanced solutions such as 3D printing, retort pouches, microwave-assisted thermal sterilization (MATS), and high-pressure processing (HPP) to improve production efficiency and product quality.
These advancements are crucial for optimizing processes and reducing production costs while ensuring the safety and durability of ready-to-eat meals. For example, 3D printing allows for intricate designs and customizable shapes, enhancing the appeal and functionality of packaging. MATS technology facilitates rapid and uniform heat distribution, preserving the nutritional content of MREs. HPP helps extend the shelf life by eliminating pathogens without compromising the taste or texture of the food. These innovative solutions are driving forces in the advancement of MRE manufacturing towards sustainability and meeting consumer expectations.
1. 3D Printing
3D printing technology is transforming MRE manufacturing through the customization of food shapes and textures, reduction of production waste, and overall streamlining of the manufacturing process.
The capability of 3D printing to produce detailed and personalized designs for MREs presents a notable advantage in the food industry. Manufacturers can address specific dietary requirements and consumer preferences by utilizing this technology, resulting in a more tailored and gratifying food experience.
Beyond decreasing material waste in production, 3D printing also enhances the entire manufacturing process by automating complex tasks that would otherwise be laborious and time-consuming. This automation boosts efficiency and productivity within the MRE manufacturing sector.
2. Retort Pouches
Retort pouches are packaging solutions that utilize heat-treated pouches to sterilize MRE contents effectively, ensuring product safety, extended shelf life, and convenient storage and transport.
These pouches offer a significant advantage in MRE manufacturing by preserving the nutritional value and flavor of the food while maintaining its quality over an extended period. Through the implementation of quality control measures and technological advancements, manufacturers can protect the contents from external contaminants and bacteria, thereby reducing the risk of spoilage. This process not only enhances the overall taste and texture of the food but also enhances the portability of MREs, making them suitable for military personnel, outdoor enthusiasts, and emergency situations.
3. Microwave-Assisted Thermal Sterilization (MATS)
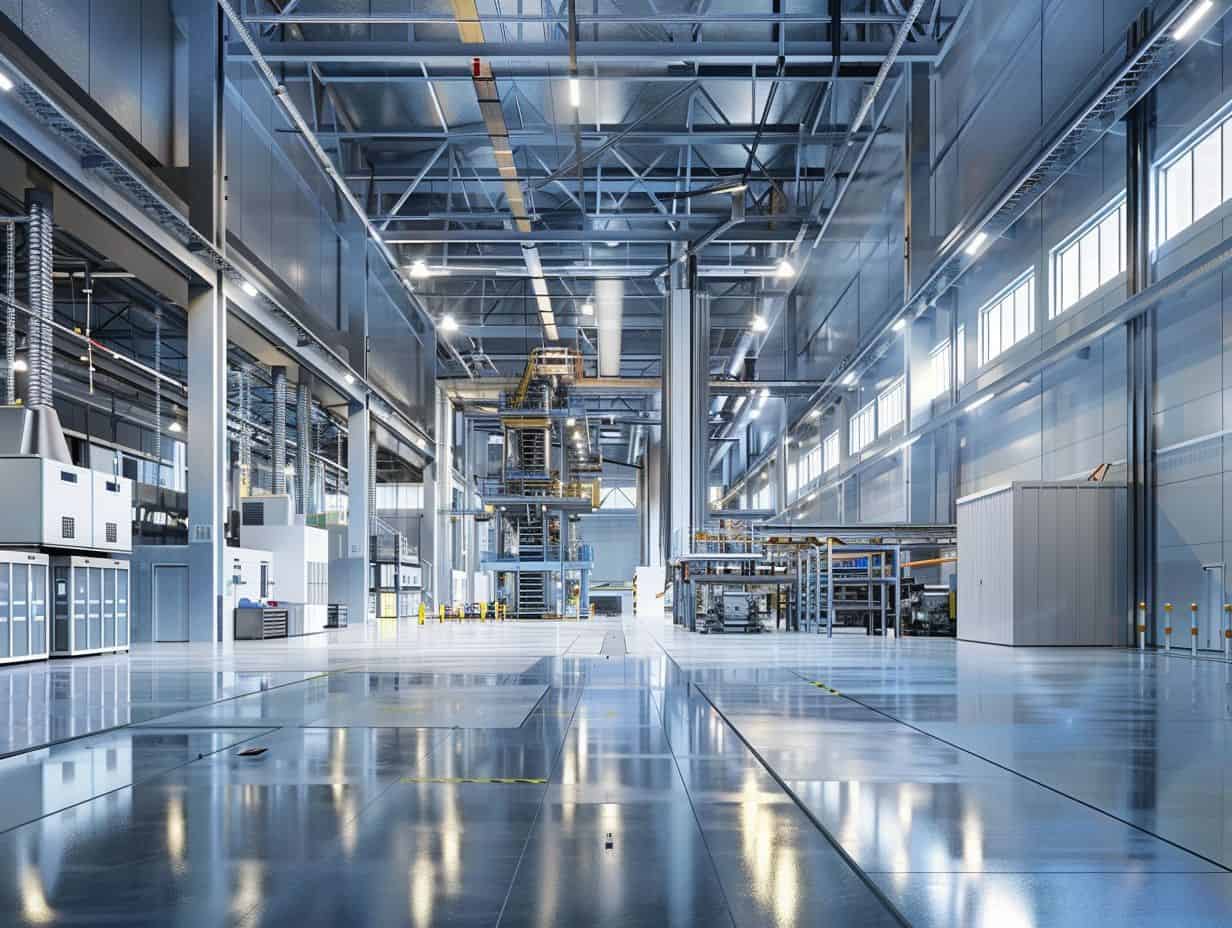
The MATS technology uses microwave energy to quickly heat and sterilize MREs, maintaining their nutritional content, flavor, and texture. This technology is crucial for improving quality control in MRE manufacturing. By controlling the heating process precisely, MATS technology reduces the risk of hot spots and ensures even cooking, leading to consistent quality in each MRE. The efficiency of MATS technology streamlines production, decreasing production times and increasing overall output.
The quick heating and sterilization of MREs enhance efficiency and optimize production schedules, helping manufacturers keep up with the demands of a rapidly expanding market. The combination of quality control, efficiency, and production optimization makes MATS technology a significant advancement in MRE manufacturing.
4. High Pressure Processing (HPP)
High-pressure processing (HPP) is a cutting-edge technology utilized in MRE manufacturing to expose packaged foods to high pressure levels. This procedure aims to eliminate pathogens, prolong shelf life, and uphold product freshness and nutritional integrity.
This innovative method plays a pivotal role in ensuring the safety and quality of MREs by effectively deactivating harmful microorganisms while preserving the taste and nutritional value of the food. HPP not only improves the efficiency of production processes but also makes a substantial contribution to sustainable practices within the food industry. By reducing food waste and decreasing the reliance on preservatives, HPP aligns with the increasing consumer preference for more environmentally friendly food manufacturing techniques.
What are the Benefits of these Innovations in MRE Manufacturing?
The advancements in MRE manufacturing technologies present several benefits, such as:
- Enhanced product quality and safety
- Increased production efficiency
- Cost-effectiveness
- Customization opportunities
- Innovative approaches to address a wide range of consumer preferences
By integrating advanced technologies into the manufacturing procedures, businesses can streamline quality assurance processes to ensure adherence to established standards and regulatory mandates. These technologies enable real-time monitoring of production activities, leading to improved operational efficiency, waste reduction, and optimal resource allocation. The capability to tailor products to suit specific market demands and individual preferences differentiates industry participants, allowing them to maintain a competitive edge. Embracing innovation strategies through technology incorporation promotes continuous enhancements and adaptability to evolving market dynamics, positioning organizations for ongoing growth and prosperity.
1. Improved Quality and Safety
The integration of innovative technologies in MRE manufacturing ensures superior quality standards, stringent safety measures, and compliance with regulatory requirements, enhancing consumer trust and satisfaction.
These advancements have revolutionized production processes by automating key quality control checkpoints, leading to more efficient and consistent outcomes. By incorporating cutting-edge machinery and software, manufacturers can closely monitor product attributes, such as texture, taste, and nutritional content, in real-time. This level of precision not only meets but exceeds industry benchmarks, ensuring that every MRE batch meets the highest quality standards. The implementation of smart sensors and data analytics streamlines operations, allowing for proactive identification of potential issues and swift corrective actions.
2. Increased Efficiency and Cost Savings
Innovative technologies play a key role in optimizing production processes, cutting operational costs, reducing waste generation, and maximizing resource utilization in MRE manufacturing. These improvements lead to enhanced efficiency and notable cost savings.
The integration of advanced process enhancements, automation solutions, and production optimization techniques in MRE manufacturing has brought about significant changes in the industry. By incorporating state-of-the-art technologies, companies can achieve increased output, better quality control, and faster turnaround times. The cost-saving measures embedded in these modern manufacturing systems not only boost operational efficiency but also lower overall production costs, making MREs more cost-effective and accessible to a broader consumer base. The result is a more sustainable and economically feasible approach to MRE production.
3. Customization and Personalization
The technological advancements in MRE manufacturing facilitate the customization and personalization of food products to align with specific dietary preferences, nutritional requirements, and flavor profiles. This, in turn, enhances customer satisfaction and loyalty.
These advancements have transformed the product development cycles for companies, enabling swift prototyping and testing of new flavors and ingredients. Through the utilization of data analytics and artificial intelligence algorithms, brands can assess consumer behavior patterns to predict trends and preferences. This allows them to shape their innovation strategies accordingly. Adopting this customer-centric approach not only cultivates a stronger connection with the target audience but also results in the development of highly tailored MRE solutions that address individual needs and surpass expectations.
What are the Challenges and Limitations of Implementing these Technologies?
The implementation of innovative technologies in MRE manufacturing presents challenges, such as initial investment costs, regulatory approvals, and ensuring consumer acceptance. One significant barrier to adopting advanced technologies for MRE production is the high initial investment costs required to upgrade equipment and infrastructure. This financial burden may be especially challenging for smaller manufacturers.
Navigating the complex regulatory landscape in the food industry to obtain necessary approvals for these technologies can be time-consuming. Consumer perceptions also play a critical role, as some individuals may have concerns about the safety and quality of products made using unfamiliar high-tech processes. The environmental impact of these advanced technologies must be carefully evaluated to ensure sustainability and compliance with eco-friendly practices.
1. Cost and Investment
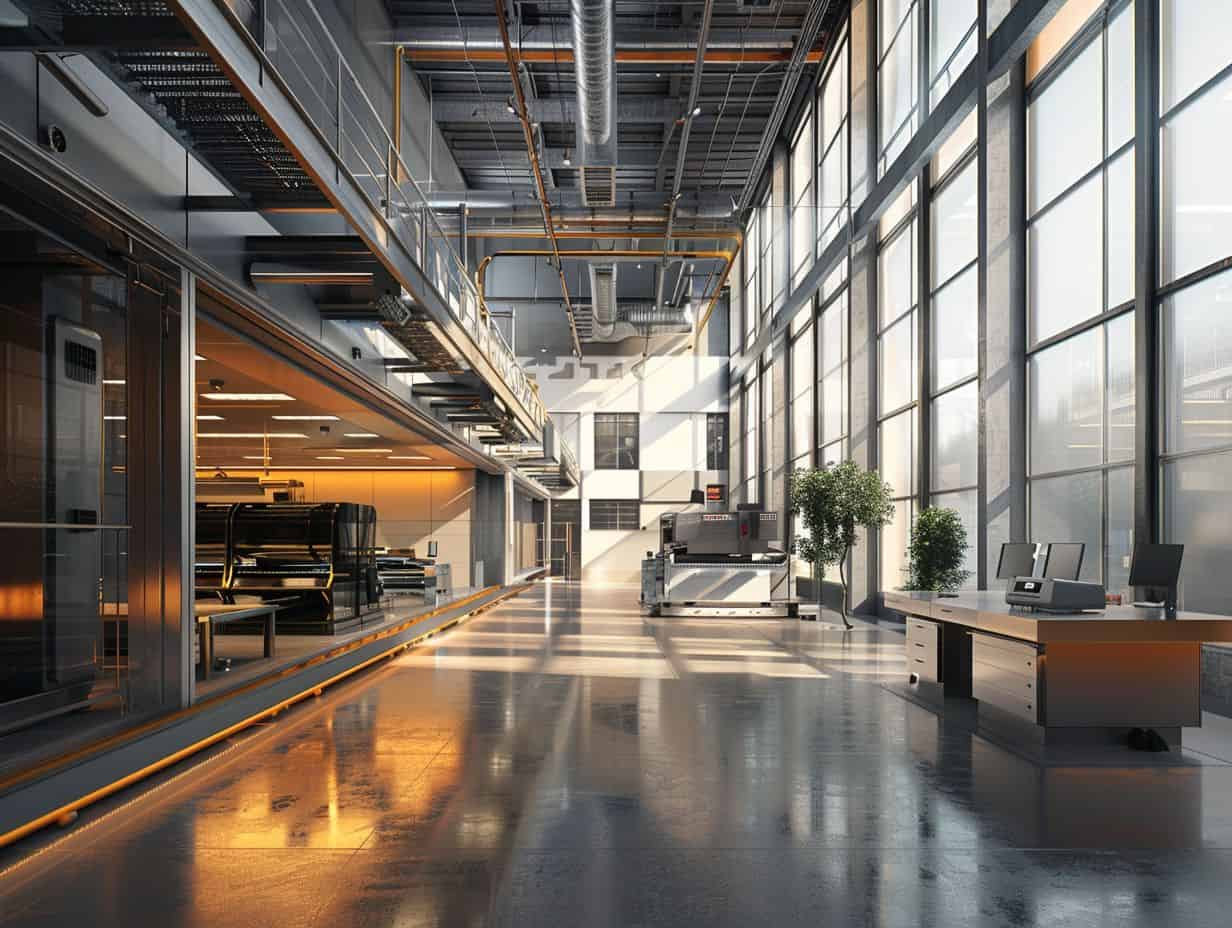
One of the main challenges in implementing innovative MRE manufacturing technologies is the significant initial investment needed for upgrading production facilities, acquiring specialized equipment, and training personnel to operate new systems efficiently.
Despite the high initial costs, adopting new technologies in MRE manufacturing can bring about substantial long-term financial advantages. By boosting efficiency and productivity, these technologies can generate cost savings in the production process. They can enhance product quality, diminish waste, and streamline operations, leading to increased profitability.
To alleviate the financial impact of investing in new technologies, companies can consider options such as government grants, tax incentives, and financing solutions tailored to support technological advancements in the industry.
2. Regulatory Approval
Obtaining regulatory approvals for innovative MRE manufacturing technologies involves thorough testing, adherence to food safety standards, risk assessments, and detailed documentation to ensure product quality, safety, and legal compliance. Navigating the intricate regulatory environment necessitates close cooperation with regulatory bodies to obtain approvals. This entails submitting comprehensive data on the technology’s safety and efficacy, conducting site inspections, and adjusting processes to conform to specific regulations. Quality assurance is crucial in demonstrating that the technology meets industry standards.
Despite the advantages of new MRE technologies, meeting regulatory requirements can be difficult due to the dynamic nature of food safety guidelines and the requirement for ongoing monitoring and updates to ensure compliance.
3. Consumer Acceptance
Consumer acceptance of innovative MRE manufacturing technologies is influenced by various factors such as product quality, taste preferences, nutritional value, pricing, and the ability to meet evolving consumer expectations for convenience and sustainability.
Customers in the current market not only look for products that fulfill their basic needs but also prioritize sustainability practices and ethical considerations in food production. To address these demands, continuous quality assurance procedures, transparent communication regarding sourcing and production methods, and a steadfast dedication to offering products that align with changing market trends are essential.
By incorporating customer feedback mechanisms and satisfaction metrics, manufacturers can customize their offerings to better align with consumer expectations, ultimately leading to increased levels of acceptance and success in the market.
What is the Future of MRE Manufacturing Technologies?
The future of MRE manufacturing technologies is expected to advance significantly by incorporating Artificial Intelligence (AI), automation, sustainable practices, and improved nutrition. These developments aim to provide high-quality, personalized food solutions that meet a variety of consumer needs and address environmental concerns.
With the rapid progress of technology, we anticipate a seamless integration of AI algorithms and automation processes that will transform the production of MREs. Sustainability efforts, such as utilizing eco-friendly packaging, implementing waste reduction strategies, and adopting energy-efficient manufacturing methods, are becoming increasingly important in the MRE industry.
There is a growing emphasis on enhancing the nutritional content of MREs by integrating functional ingredients, fortification techniques, and innovative food processing approaches to offer consumers healthier and more balanced meal choices.
1. Integration of Artificial Intelligence and Automation
The integration of Artificial Intelligence (AI) and automation in MRE manufacturing processes offers the potential for increased operational efficiency, real-time data analysis, predictive maintenance, and adaptive production capabilities to optimize resource utilization and improve product quality.
By utilizing AI algorithms, manufacturers can streamline forecasting, production scheduling, and inventory management, resulting in reduced downtime and improved collaboration among different departments. Automation speeds up repetitive tasks and maintains precise quality control through continuous monitoring and adjustments. These advancements lead to cost savings and enable the development of more agile and responsive production environments that can swiftly adjust to evolving market demands.
2. Sustainable and Eco-Friendly Solutions
The future of MRE manufacturing aims to incorporate sustainable and eco-friendly solutions that focus on resource efficiency, waste reduction, recyclable packaging, and energy conservation to minimize the environmental impact and support long-term sustainability.
This shift towards sustainability in MRE production includes the adoption of innovative technologies, such as renewable energy sources and efficient manufacturing processes, to reduce greenhouse gas emissions and water usage.
The implementation of closed-loop systems and circular economy principles further improves sustainability efforts by maximizing material reuse and decreasing overall waste generation. By integrating sustainable practices throughout all production stages, from raw material sourcing to distribution, the industry can achieve a more environmentally conscious approach that benefits both the planet and future generations.
3. Improved Nutrition and Health Benefits
Future MRE manufacturing technologies are focusing on improving nutritional content, incorporating functional ingredients, offering allergen-free choices, and accommodating dietary preferences. These changes aim to offer healthier and more nutritious meal options that meet consumer expectations for balanced diets and well-being.
These advancements in MRE production not only respond to the increasing demand for convenient, high-quality meals but also emphasize health and wellness by integrating advanced technologies. The goal of these innovations is to enhance the nutritional value of each meal, ensuring that consumers receive necessary nutrients and energy from their food.
By utilizing state-of-the-art methods and quality control procedures, manufacturers can provide customizable options that cater to a range of dietary needs and preferences while maintaining optimal taste and texture.
Frequently Asked Questions
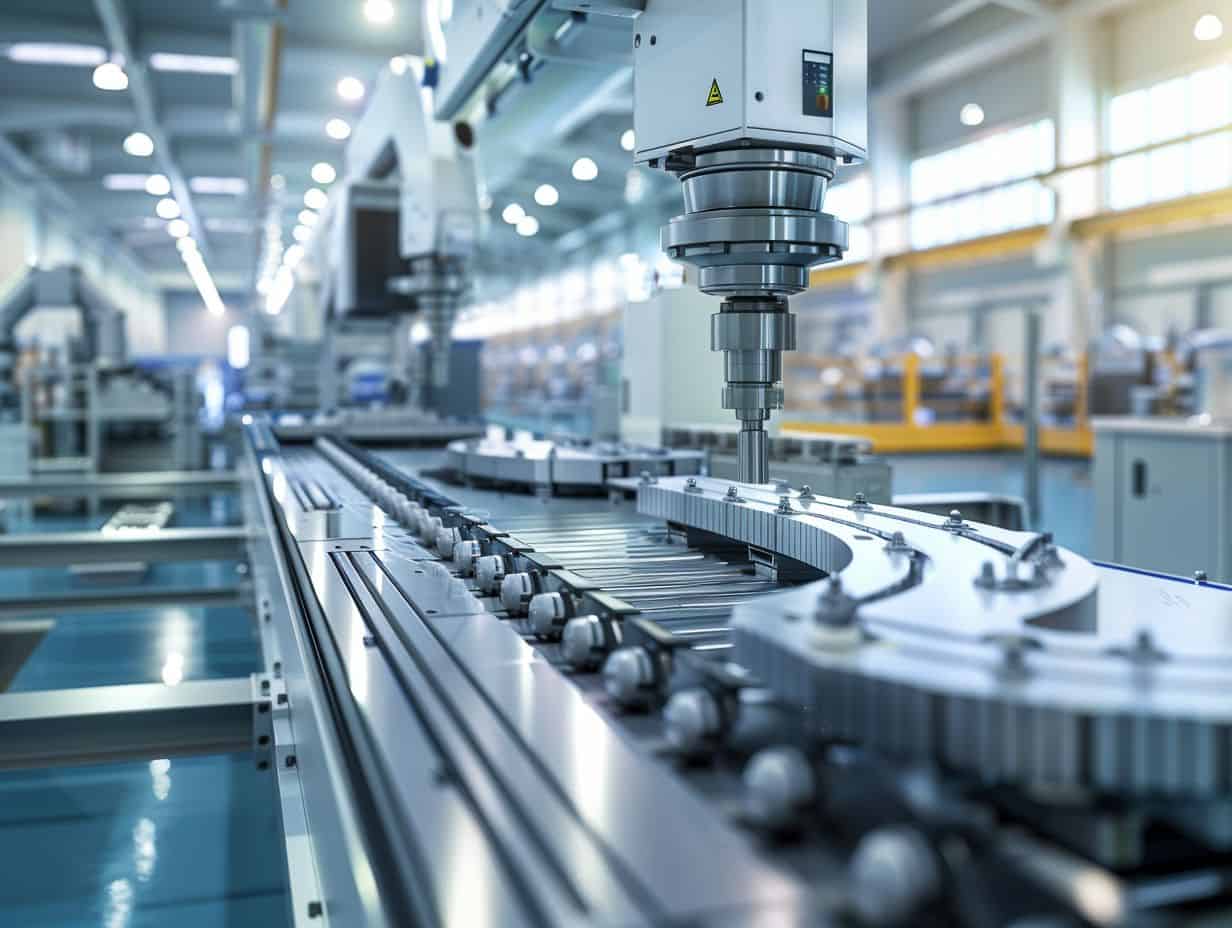
What is Continuous Improvement in MRE Manufacturing Technologies?
Continuous Improvement in MRE Manufacturing Technologies is an ongoing process of making regular improvements and advancements in the way meals ready-to-eat are produced, packaged, and distributed.
Why is Continuous Improvement important in MRE Manufacturing Technologies?
Continuous Improvement is important in MRE Manufacturing Technologies because it allows for increased efficiency, cost-effectiveness, and quality control in the production and distribution of MREs. It also allows for the incorporation of new and innovative technologies to improve the overall product.
What are some examples of Continuous Improvement in MRE Manufacturing Technologies?
Some examples of Continuous Improvement in MRE Manufacturing Technologies include the development of new packaging materials to increase shelf-life, the integration of automation in production processes, and the use of advanced food preservation techniques.
How does Continuous Improvement benefit consumers of MREs?
Continuous Improvement benefits consumers of MREs by providing them with a higher quality and more consistently produced product. It also allows for a wider variety of options and flavors to be available, and can potentially lead to lower costs for the consumer.
How does Continuous Improvement impact the environment in MRE Manufacturing Technologies?
Continuous Improvement in MRE Manufacturing Technologies can have a positive impact on the environment by reducing waste and energy usage through more efficient production processes. It also allows for the development of more sustainable packaging materials.
What are some future innovations that can be expected in MRE Manufacturing Technologies through Continuous Improvement?
Some future innovations that can be expected in MRE Manufacturing Technologies through Continuous Improvement include the use of 3D printing for food production, the incorporation of sensor technology for real-time monitoring of food quality, and the development of personalized nutrition options within MREs.